事業概要
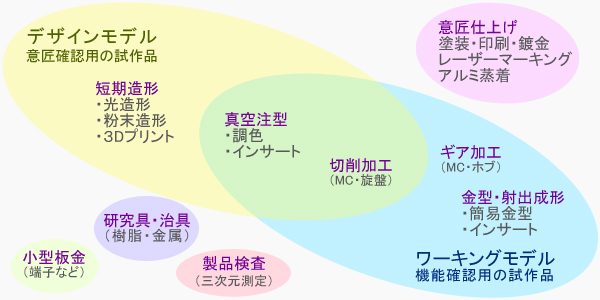
当社は「試作専門の会社」で今まで数々のデザインモデル・ワーキングモデルの製作を手掛けて参りました。
「試作=量産前提の製品」であると十分に認識し、量産までの工程においてお役立ていただける高品質な製品の製作に努めております。また、コスト面や納期面につきましても、できる限り柔軟に対応させていただきます。
これまで、航空機分野・自動車分野・OA機器分野・弱電分野・医療分野・産業機械分野における試作モデル・部品の納入実績があり、ワーキングモデル(試作部品)の品質・精度はもちろん、特にデザインモデル(意匠品・外装品)における仕上がりは、各分野のお客様にご好評いただいております。
試作モデル・試作部品の製作がおありでしたら、ぜひ当社へご用命ください。
プラスチック試作のいろいろな加工方法
安く早くならコレ!光造形(SLA)
通常工期 | 手の平サイズで3~6営業日 |
寸法公差 | 中級~粗級 |
主な材料 | 紫外線硬化エポキシ樹脂 |
取扱材料 | SCR735(ABS相当)、TSR821(強靭性) |
工法・概要 | 紫外線レーザーを照射することで硬化するエポキシ系樹脂を、0.1mmの厚みで重ねて、造形を行う方法 |
加工工程 | プログラミング→光造形→荒仕上(サポート除去)→本仕上げ(外観面の積層除去)→コーティング(塗装) |
マシンテーブルサイズ | 580×480×490 mm |
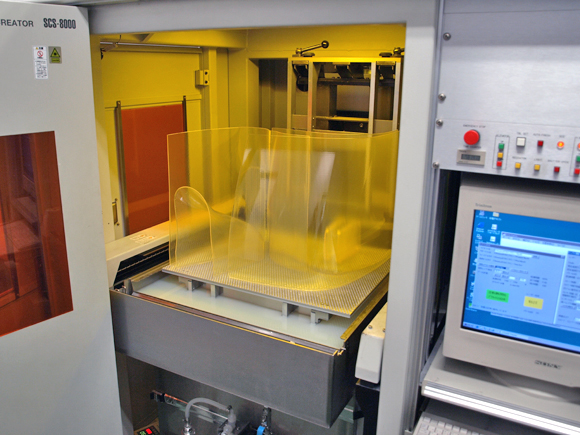
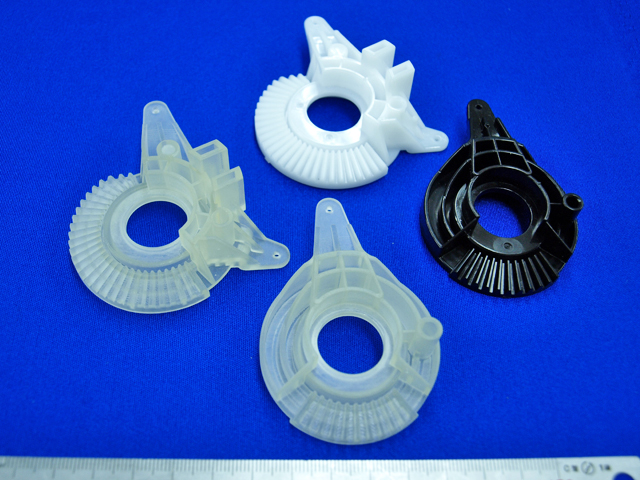
【特徴】
光造形の工程は深夜稼働も可能なので、切削加工に比べ工期が短く、また安価なのが一般的です。積層方式なので、アンダーカットがある形状も一体加工ができることが特長です。光造形の通常の積層ピッチは0.1mmです。一般的なコピー用紙の厚みも0.1mmなのですが、ちょうどコピー用紙を数十枚重ねた際の側面のガタガタの様な形状が、光造形品の側面にも出てきます。これを積層目といいます。この積層目を除去する場合はそれなりの手間と時間を要し、この作業を本仕上げといいます。荒仕上まででしたら、かなりコストを抑えられます。本仕上げは、その程度によっては価格も上がります。
積層方向に割れやすいので(壊れやすいので)製品に力があまり掛からない、形状確認用の試作に適しています。また吸湿性があり、熱に弱いという弱点を持ちます。メッキ処理は不可ですが、塗装や染色は可能です。
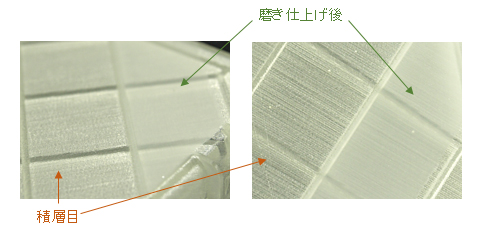
加工方法の比較
工法 | 工期 | 精度 | メリット・特長 | デメリット・注意 |
---|---|---|---|---|
光造形 | 3-6営業日 | 中級 | 工期が短い 切削品より安価 | 壊れやすい 熱に弱い |
粉末造形 | 3-6営業日 | 中級 | 耐熱靭性に優れる 工期が短い | 表面がザラザラ 吸湿性がある |
3Dプリント | 3-6営業日 | 中級 | 彫刻形状に最適 工期が短い | 光造形よりコスト高 大きな造形が苦手 |
切削加工 | 5-7営業日 | 精級 | 試作の定番工法 精密加工 | 形状によっては分割&接着もしくは対応不可 |
真空注型 | 10-14営業日 (マスター含む) | 中級 | 複数個ならコストメリット有 インサートや調色も可 | 材料が限定される 形状によっては対応難 |
試作金型 射出成形 | 14営業日~ | 精級 | 本型より工期早め 量産材料で成形可 | 綿密な打ち合わせが必要 形状により対応不可 |
※上記はあくまで“感覚値”です。工期や精度を保証するものではありません。
※工期は小物~手の平サイズのワークを想定。
工期の比較
光造形・粉末造形・3Dプリントは、いずれも工法は積層方式です。積層方式なので、アンダーカット部も難無く形状化できるところが特徴です。概略としては「3Dデータを提供いただく→機械に掛ける」の工程なので、小物~手のひらサイズのワークであれば、切削加工に比べ早く仕上がる場合が多いです。ただし、ワークサイズが大きいものや、とても複雑な形状、数量が多い、仕上げ(磨き)に時間が掛かるものは、工期が長くなる場合もあります。
真空注型は、光造形または切削加工でマスターを製作してから注型工程に入るため、工期は長めになります。ただし、個数が多い場合は、真空注型の方が工期が短くなる場合もございます。
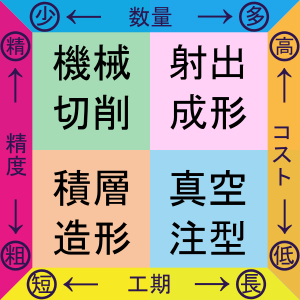
精度の比較
精度が求められるのであれば、切削加工もしくは金型+射出成形を提案致します。切削加工機の精度は“精級”です。光造形でもソコソコの精度が出ますが、光造形の材料は吸湿性があるため、保管環境によっては形状変化(湿気による膨張など)が起こりえます。
真空注型は精級を狙って加工致しますが、マスターおよびゴム型は加工環境・使用環境の影響(温度・湿度)を受けやすいため、精度“中級~粗級”でお考えいただいた方がいいかもしれません。
精度目安 | 0.5-3.0 | 3.0-6.0 | 6.0-30 | 30-120 |
---|---|---|---|---|
精級 | ±0.05 | ±0.05 | ±0.1 | ±0.15 |
中級 | ±0.1 | ±0.1 | ±0.2 | ±0.3 |
粗級 | ±0.2 | ±0.3 | ±0.5 | ±0.8 |
※精度の表は「精級~粗級」の感覚値をご覧いただくものであり、寸法公差を保証する内容ではございません。
※表は「JIS B 0405:1991」より一部抜粋